Blog Post 5 - AA
- Anagha Arvind
- Oct 14, 2019
- 3 min read
Author: Anagha Arvind
Date: October 13, 2019
Group Members: Adin Field, Gordon Ellis, Jordon Bibian, Anagha Arvind
Blog Contents:
1. Prototype Designs
2. Initial Prototyping strategy
3. Eventual Manufacturing for Scaling up Production
4. Additional interviews
The group met during the week to decide the initial prototype designs and strategies in order to figure out what the prototype would look like, and how we would begin the prototyping process.
1. Adin created a functional analysis block diagram, which we used to determine what materials we would need, what requires CAD models, and what type of software we would need.

Current Materials (from external manufacturers)
Arduino Uno
Breadboards
Blood pressure cuff
Pressure Transducer
Various electronic components
Power Supply/ Rechargeable battery
Speakers
Microcontroller
MAX30102 High Sensitivity Pulse Oximeter and Heart-Rate Sensor for Wearable Health
LM-35 sensor
Connecting Wires
etc...
2. Jordon came up with a potential look of the product’s display. The main vitals such as heart rate and blood pressure are displayed in English and Swahili. Additionally, there is a dosage amount and time recommendation to be used as guidance for the person delivering the anesthesia. There is also an alert (loud noise and flashing) that will go off when the vitals are abnormal. There are additional features that will be shown in the display, such as pulse oximetry and body temperature. There will also be a window in which nurses can input patient information such as height and weight, in order to get the right anesthesia dosage.

The initial prototyping strategy that the team decided for the first iteration was to use milling to create a carrying case for the vitals monitors and display and parts of the display itself through milling. Milling uses the subtraction of material from a larger piece of material, using a milling machine and a fixture. The carrying case is a rather simple design to model and create. The reason this method was used, compared to 3D printing, is that it takes significantly less time to mill the carrying case than 3D printing it, according to Jordon. The group is still deciding the material that we should use, perhaps plastic, as long as fits the product design specification of not being very heavy (<10lb). A majority of our product requires computer and electrical expertise. The group has decided to use Arduino Unos and various online tutorials to create the vital sensing monitors. These resources will be used to create a circuit block diagram of all the components put together. For the initial prototype, we will use a cardboard box for the case and strings for wires to demonstrate this, as we are going for looks and not functionality at the moment.
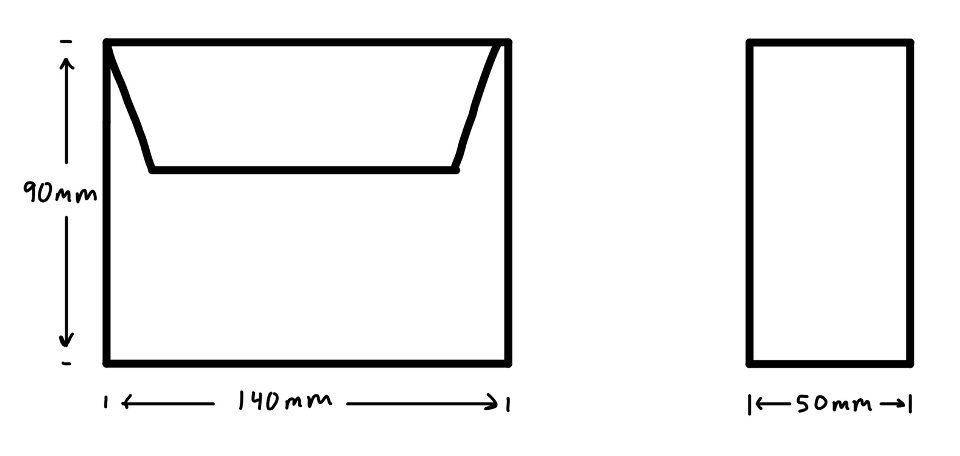
3. For the eventual Manufacturing for Scaling up Production, the group decided to use injection molding in order for the product to be mass produced. This also means the material we would use would be plastic. The advantages of this procedure is that it is a rather efficient, good quality method that produces low scrap rates. This is beneficial especially in low resource settings, as the process is repeatable and can produce multiple parts in succession. In doing so, more nurses will have access to anesthesia monitoring and delivery guidance, making it easier for more minimally trained nurses to aid with important surgical procedures. This topic shall be discussed further and can be subject to change to a different option for manufacturing of scaling production.
4. The group is still working on interviewing more stakeholders. We were in correspondence with one of the anesthesiologists at UMass Worcester hospitals: Dr. Shekhar. She said there is a possibility of an observation, however the group has since found out that is not possible. We are in the process of speaking to a few people she has referred to.
Yorumlar